5 min read
What Is Logistics, And How Can It Kickstart My Career?
Amy Lawrence
:
Feb 23, 2020 9:00:00 PM
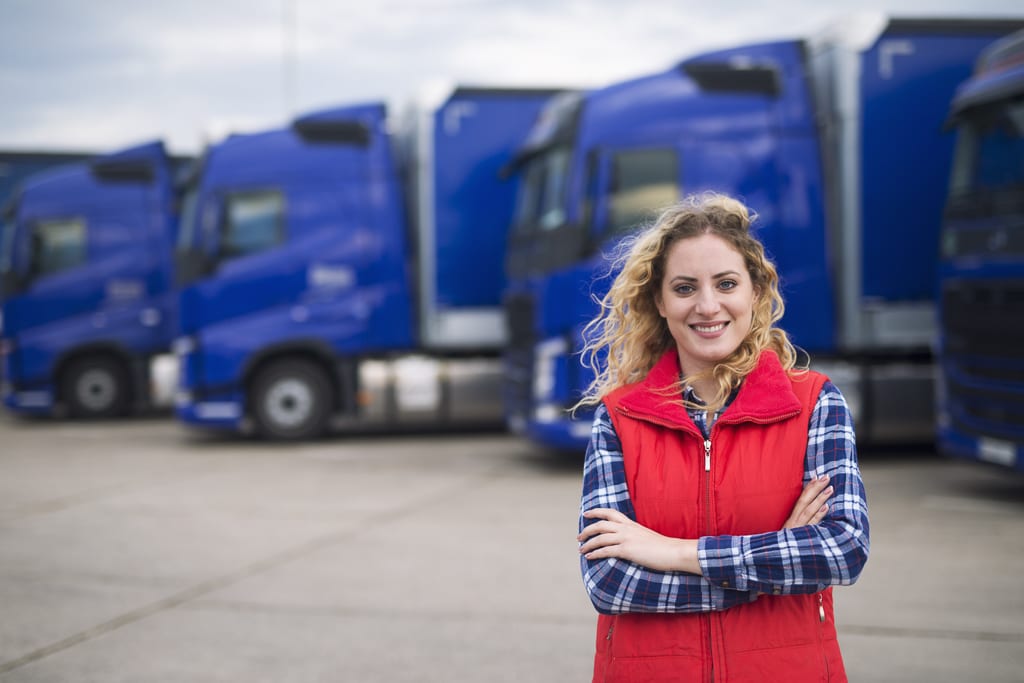
“Logistics” is a word you may have heard many times but never given thought to. In reality, logistics is all around us. Whenever we buy something from a store, order things online, or even drive past a huge semi truck on the highway, we are encountering logistics in some way.
What is logistics? In simple terms, it’s the word used to describe the flow of goods from their point of origin to the point that they will be “consumed,” or bought. You can think of it as the part of supply chain management that involves moving things around.
Because logistics is needed to make sure that the products we use every day arrive at store shelves — or, more and more often, on our front porches — it is a huge part of what makes the modern world tick.
As the amount of people on earth grows and the amount of goods we consume does, too, logistics will become more and more complex into the future. In turn, demand for skilled laborers who have been trained in the basics of logistics will increase.
What kind of careers use logistics? Tons! Truck drivers are assigned routes according to logistics. People who work in warehouses need logistics in order to function, especially if they’re selling things online. Even someone who works in customer relations, retail management, or displays and stocking must understand logistics in order to do their job better.
The types of logistics jobs available will increase and become more complex over time. People who want to get a job that doesn’t require a bachelor’s will need to know about the principles of logistics to drive trucks, work at warehouses or loading docks, or be effective in the retail environment.
In short: learning about the basics of logistics at an employment training program near you can potentially put you on a path to a better job with better pay and more responsibilities.
Logistics Explained
Logistics is a fancy-sounding word because it was invented by French and British military strategy experts in the late 1800s. Military logistics involved getting supplies like food and ammo to your troops on the front line. Often, logistics experts needed to figure out how to get these supplies across areas that didn’t have roads — or areas that were well behind enemy lines.
In fact, “logistics” used to be a word that applied only to military operations until the early 20th century. Around that time, businesses started selling things in retail environments farther and farther away from the goods’ point of origin.
Whereas 200 years ago you would buy your shoes, shirts, and laundry soap from someone who made it in your own town, about 100 years ago that started changing. The industrial revolution made it possible to produce a huge amount of goods all at once and at a cheaper price. Railroads and, later, cars, made it easier than ever to ship the goods to destinations farther from the point of origin.
Now, almost nothing we buy was made in the same city or town in which we live. In fact, it’s likely that it was even made in the same state — or country!
Bigger businesses shipping larger loads with more types of goods to more customers than ever meant that it became tough to make decisions. Business logistics experts were needed to answer questions like:
- How can I make sure this shipment of flour makes it to San Jose before it spoils?
- How can I send these shoes made in Vietnam to 50 different U.S. states as cheaply and quickly as possible?
- How should I route these orders for 20 different products the best way to minimize cost and possible damage while still meeting deadlines?
- How often should I order this specific product so our store shelves don’t run out, but we don’t have a ton of overstock taking up room in the back?
- How many truck drivers should we hire to meet our shipment deadlines every month without having more employees than we need?
- How should we handle online orders so that they can be packed and shipped quickly to the right customer without any mistakes?
The answers to logistics questions sit at the heart of the modern consumer experience. If the answer is wrong, hundreds — sometimes millions — of people could be upset. Businesses could also stand to lose a ton of money.
Because of the importance of logistics and the rise in physical and especially online retail, logistics has become something that touches thousands of different jobs and careers.
What Are Types of Logistics Jobs That Don’t Require a Bachelor’s?
Many types of logistics jobs demand advanced skills in math, computer science, and supply chain management. People who get advanced degrees in logistics or logistics-facing fields can often command huge salaries, sometimes in the six digits!
But you don’t have to get a Master’s or even a Bachelor’s to benefit from logistics training. Many well-paying jobs can be earned just by obtaining basic logistics knowledge at an employment training program near you.
Examples of jobs that involve logistics that don’t require a four-year or advanced degree include:
Truck Drivers
Truck drivers are like the red blood cells of our economy. Just like every cell needs the oxygen red blood cells bring them to survive, every retail business and customer needs regular truck shipments.
According to the American Trucking Associations, trucks traveled 297.6 billion miles in 2017.
While it may seem like a truck driver simply has to drive the routes they’re given, understanding logistics will make them more effective and make their job easier. Assignments are often based on complicated time tables and order invoices. If a truck driver knows what everything on their paperwork means, they will be able to catch potential mistakes or spot opportunities for more efficient routing.
Because of this connection, every truck driver training course includes some of the basics of logistics and supply chain management.
Inventory Control
Inventory control specialists aim to keep shelves stocked while also keeping costs low. Their goal is to make sure that all customers get what they need.
At the same time, they don’t want to ever order more than they would need. Doing so can mean too much space in the warehouse is taken up. Other times, demand for the goods will drop, and the retailer will have to sell the remaining stock at a loss. Some goods will spoil if they sit too long.
As a result, understanding logistics and supply chain management is essential for anyone involved in inventory control. This can be someone assigned inventory control and ordering as a specific job or a retail manager or supervisor responsible for inventory ordering.
Shipping and Receiving Operations
Nearly every business has some amount of shipping and receiving. Logistics, naturally, controls the flow of goods through these departments. Understanding logistics helps a shipping and receiving specialist staff for their shift and organize inventory more effectively. It can also aid them when it comes to predicting patterns, ensuring that they don’t get caught off guard when activity suddenly surges in their department.
Customer Relations
“Why isn’t my order here yet? How long before my broken item is repaired and returned to me?” Questions like these seem like they should have easy answers on the customer’s end of the phone, but the customer relations specialist could have no clue — unless, of course, they are keyed into their employer’s logistics.
Understanding logistics, therefore, can make you a more effective customer relations associate or manager. It helps you not only deal with individual customer issues, like the examples above, but also predict how things will go so that you can keep lots of customers — or businesses that place large orders regularly — happy.
Merchandising, Displays, and Stocking
A lot more goes into stocking shelves and setting up displays than merely making things look pretty. Stocking levels and promotional displays are almost always determined by patterns in logistics.
For example, a company that has a surplus of a certain item like deodorant may want to promote that item to reduce overstock. Or, a seasonal item should be displayed in a certain way so that it can sell out before the relevant holiday or seasonal period is over.
Store managers and stocking specialists have to understand logistics in order to be more effective at accomplishing their retailer’s goals. It also gives them information they can use to make smarter decisions that could, potentially, advance their career.
Forklift Operation and Certification
If trucks are red blood cells that bring other cells oxygen, then forklifts are like the proteins that move things around in cells to keep them functioning. That may be too nerdy of an analogy, but it does show how we might take the work of forklifts for granted in terms of how crucial they are to keeping supply chains going.
Logistics tells forklift operators what needs to be moved when and to where. For those who work in smaller operations or have more responsibility, they will need to make decisions on how to route, organize, and schedule movements of stock in order to keep up with schedule demands.
Logistics Keeps Our World Moving
As you can see, logistics is an incredibly important part of truck driving and other retail jobs. Learning the basics of logistics at an employment training course near you could be an important step in earning different types of logistics jobs — and kick-starting your new career!
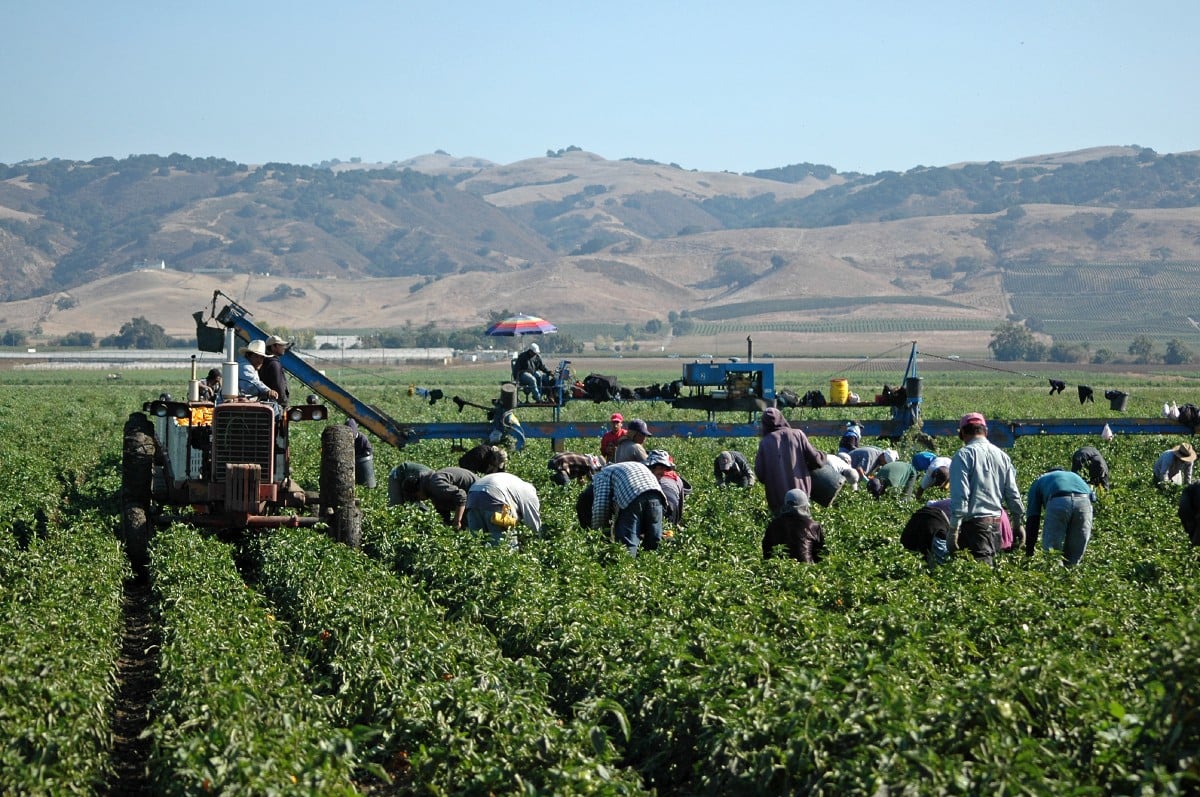
Welding Together a Better Future: A National Farmworker Jobs Program Success Story

The National Farmworker Jobs Program (NFJP) is a valuable program from the U.S. Department of Labor that’s empowering farmworkers across the country...