
Cement has been used by humans for thousands of years. In fact, one of the reasons so many buildings from ancient Rome are still standing is because they created an incredibly strong concrete that we still can’t replicate today.
Today, concrete is the most widely-used manmade material, but Portland cement accounts for at least 5% of all greenhouse emissions. There is a type of concrete that can be used for green construction, magnesium oxychloride cement (MOC). However, until recently the poor water resistance of this green cement made it an unviable material.
Now, a new water-resistant version of MOC has emerged as the frontrunner for a usable green cement. That means lower emissions for the construction industry — and new knowledge for those who are receiving job training for green construction.
What Is MOC?
Magnesium oxychloride cement (MOC) is created by mixing magnesium oxide with a solution of magnesium chloride. Both of these substances are byproducts of mining for magnesium, meaning these substances aren’t wasted or leaked into the environment. Both magnesium oxide and magnesium chloride are plentiful in a variety of countries like Australia and China.
The fact that these potentially dangerous substances are taken from the environment makes MOC a green cement. But magnesium oxide also captures carbon dioxide from the atmosphere, furthering its carbon-neutral trait.
MOC isn’t just a green cement, it’s also a superior material when compared to conventional varieties like Portland cement. It has more compressive strength than regular cement, and it sets very fast. Unfortunately, MOC’s strength will degrade severely with prolonged contact with water. As such, its main use was indoor applications — until now.
How Water-Resistant MOC Was Developed
Researchers in Australia have been working on a water-resistant version of MOC since 2017. They added other industrial byproducts like silica fume and fly ash, a byproduct of the coal industry, along with industrial chemicals, to develop water resistance. Both fly ash and silica fume filled in pores in MOC, making it denser, stronger and more water resistant.
Unfortunately, the MOC’s strength would still disintegrate under warm water, so the researchers added phosphoric acid and soluble phosphates. This greatly improved resistance to warm water. Now, MOC has a greater compressive strength and flexural strength than conventional cement. It can retain its strength after being soaked in water for 28 days. Even if it’s soaked in warm water for 28 days, it can retain 90% of its strength.
How Will Green Cement Impact the Construction Industry?
Now that MOC has been proven to be a viable green cement, even when wet, the big question is if it will replace traditional cement. With the current green construction push, there’s a good chance that this more environmentally-friendly concrete will become more prominent in the industry. However, using MOC may be more technical than using traditional cement. Time will tell if it will totally take over the industry, but learning how to use MOC as part of job training for green construction would be a great idea.
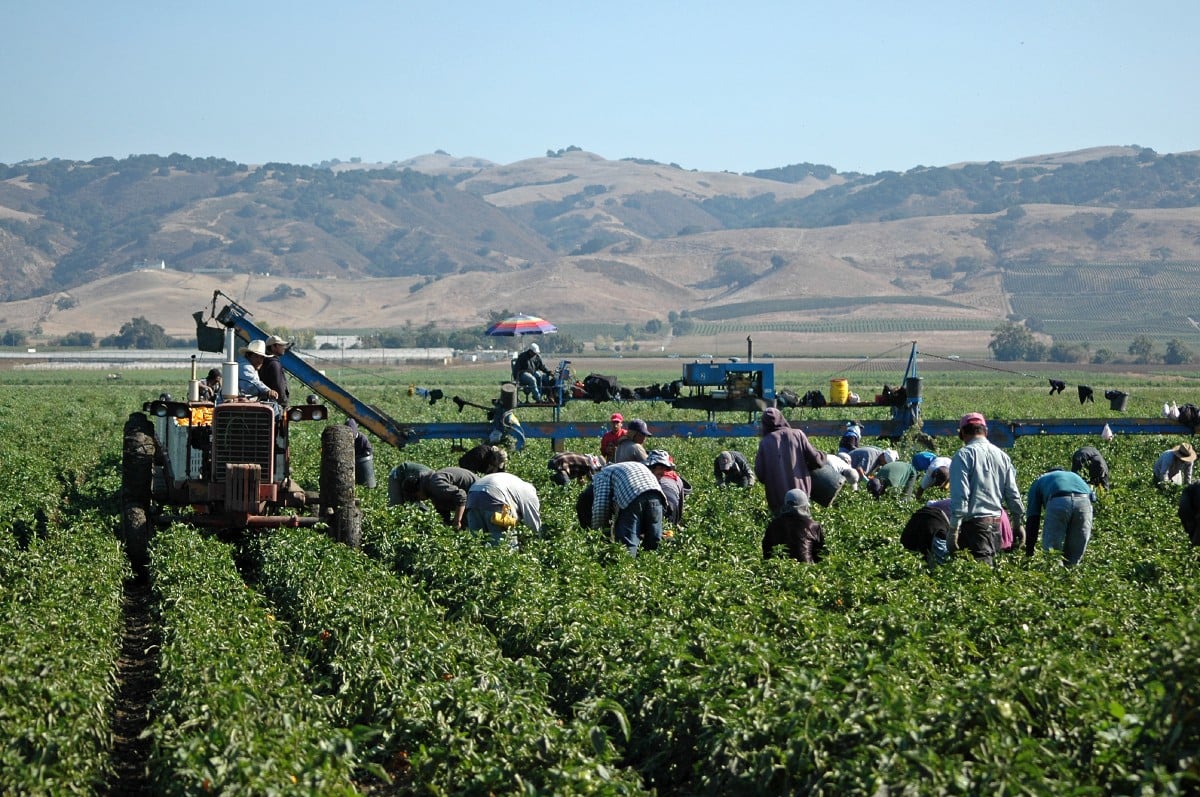
Welding Together a Better Future: A National Farmworker Jobs Program Success Story

The National Farmworker Jobs Program (NFJP) is a valuable program from the U.S. Department of Labor that’s empowering farmworkers across the country...